The manufacturing industry has evolved over centuries — from human-centric processes to machine-centered assembly to the highly automated companies we’re seeing more of today.
Manufacturers are leveraging several tech innovations to revolutionize the manufacturing industry. Together, the technologies are called the Fourth Industrial Revolution or Industry 4.0. The revolution started at the beginning of the century, with the intention of helping manufacturers develop self-sustaining systems that are:
- Flexible enough to optimize performance
- Highly adaptable to change
- Capable of learning from existing conditions
Here are the five biggest technologies that have been driving the revolution in manufacturing for the past two decades.
1. Industrial Internet of Things (IIoT)

Industrial Internet of Things (IIoT) is the interconnection of sensors, instruments, and other devices in the factory setting with the end goal of collecting data. Manufacturers use the data they collect with IIoT to enhance manufacturing processes.
Sensors and actuators are prime examples of interconnected IIoT devices. The sensors and actuators on the factory machine gather data to help manufacturers:
- Understand how machines are performing
- Reduce machine downtime
- Optimize maintenance process
- Predict when the machine might fail
The driving philosophy behind IIoT is that smart machines are better than humans at capturing and analyzing data in real-time. As a result, IIoT technology communicates vital information to drive business decisions faster and with a higher accuracy.
According to Statista, over 55% of manufacturers leveraging IIoT saw reduced operational costs that stemmed from the following:
- Improved equipment uptime and availability
- Increased operations speed
- Easy product tracking throughout the supply chain
- Predictive maintenance because the IIoT systems predict when a machine will need to be serviced
- Improved facility management
2. Predictive Maintenance
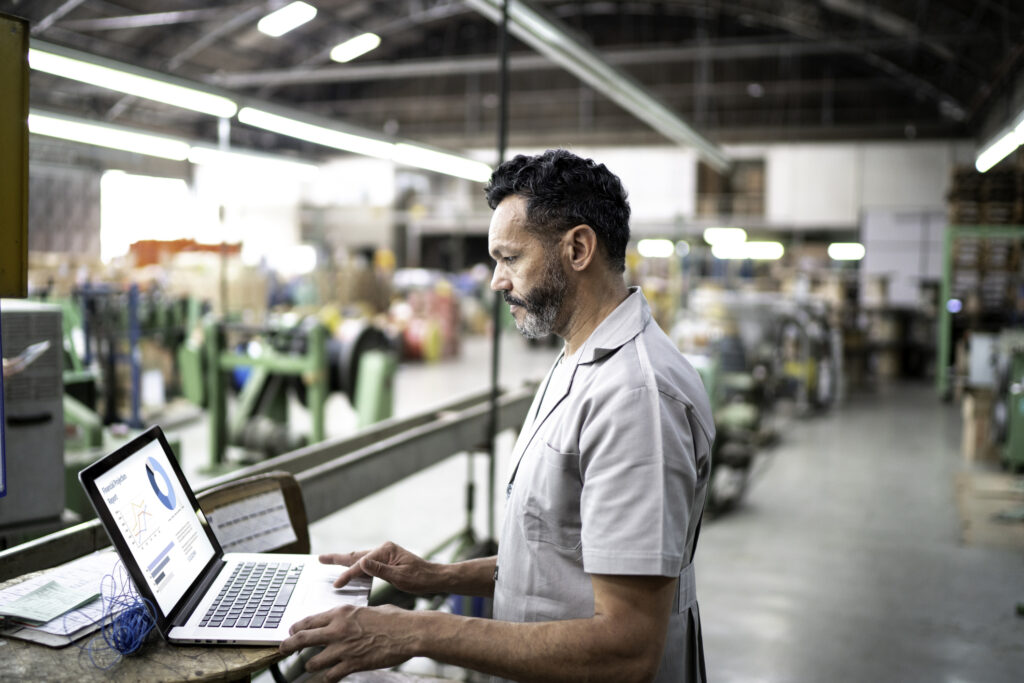
Predictive maintenance in manufacturing is the use of data from sensors and artificial intelligence (AI) to detect failure patterns in machines and components.
Manufacturers are deploying technology that can execute predictive analytic work. The tech includes:
- Sensors that collect device-level data
- Analytics tech that interprets machines’ condition, detects irregularities, and fixes issues before machine failure
The idea behind predictive maintenance is that when manufacturers understand when a machine or part is likely to fail, they can take preventive action and maintain their equipment more effectively.
Studies project a return on investment of 10X the original expenditure. Many might think the returns are impossible, but the costs related to unexpected equipment failure are staggering. The estimated downtime cost is around $250,000 per hour for a company.
The cost includes:
- Discovery expenses
- Containment costs
- Recovery from failure
- The cost associated with lost productivity
- Supply chain disruption
However, the cost excludes equipment repair or replacement expenses.
Since 80% of manufacturing companies experience unexpected downtime, manufacturers should prepare. Predictive maintenance technology can dramatically cut down unexpected downtime.
3. Artificial Intelligence and Machine Learning (AI/ML)
AI and machine learning are intrinsically connected with IIoT. Process manufacturing is a highly competitive sector, with swiftly-changing markets and complex systems with many moving parts.
To improve profitability and drive innovation, many processing plants leverage all advantages that AI and ML can give. Manufacturers use AI and machine learning to integrate data, analyze it, and produce deep insights and predictions that help drive decisions.
Manufacturers use machine learning to crunch huge datasets to spot patterns and trends. Then they use the information to build algorithms that predict what will come in the future. Manufacturing companies use AI and machine learning to:
- Cut waste and find new efficiencies
- Understand market changes and trends
- Increase product quality
- Meet industry standards and regulations
- Improve product quality because AI can alert companies to problems in the production line that can result in quality issues
According to a recent survey, 50% of manufacturing companies using AI and machine learning will have the potential to double their cash flow over the next five to seven years.
4. 5G and Edge Computing
5G is a game changer in IIoT deployment because it allows faster, more secure, and more stable connectivity. The development of 5G promotes the deployment of IIoT because it improves the performance and reliability of the connected device.
The commercial success of any IIoT depends on its performance, which is tied to how quickly interconnected devices can communicate. The 5G will improve data transfer speeds, allowing manufacturers to leverage the data collection and processing within devices such as sensors or smart machines.
Manufacturing companies can create private 5G networks on their premises to give them superfast data speed without needing cables or much-improved data security.
5G will also be critical for predictive maintenance in the company, as it involves a large amount of streaming data that manufacturers want to track and analyze.
5. Robot Aides
Speeding up development is a huge priority for most manufacturers. One critical part of automation is the use of robots.
While robotics in the manufacturing sector is gaining traction, many don’t use robots to replace human workers, but to enhance human work. Manufacturers use factory robots to execute tasks that require greater precision levels, increased speeds, and patience.
Using robots in the manufacturing process accelerates the production process. A recent report by PwC says that 59% of manufacturing companies utilize at least one type of production robot.
Most manufacturers resort to robot aides to:
- Protect the human workforce from risky, filthy, or monotonous tasks
- Enhance product quality and prevent mistakes
- Minimize inconsistency in a produce
- Lower production costs
The Future of Manufacturing is Yours with Technology
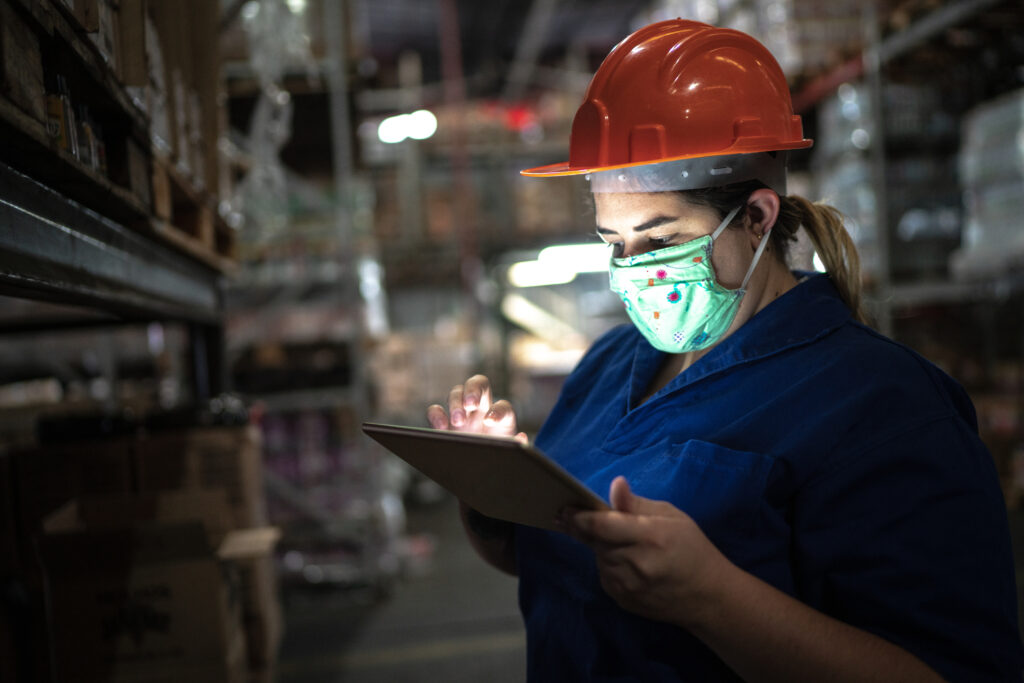
Smart use of technology is an integral part of success in manufacturing today. To maintain a competitive edge, manufacturers should invest in technologies that can move them toward smart factories.
Manufacturers need to:
- Understand and embrace evolving technologies to increase their business value
- Identify technologies that enable them to achieve efficiency and agility, and improve customer experience
- Leverage insights from the technology they deploy to reduce time and material costs, optimize resources, and engage customers, employees, and suppliers.
Manufacturers need to look beyond short-term costs to the long-term benefits of a digital transformation. The only existing problem with implementing manufacturing technology is the threat of cyber attack, technical difficulty integrating technology into the factory, and reluctance to implement automation.